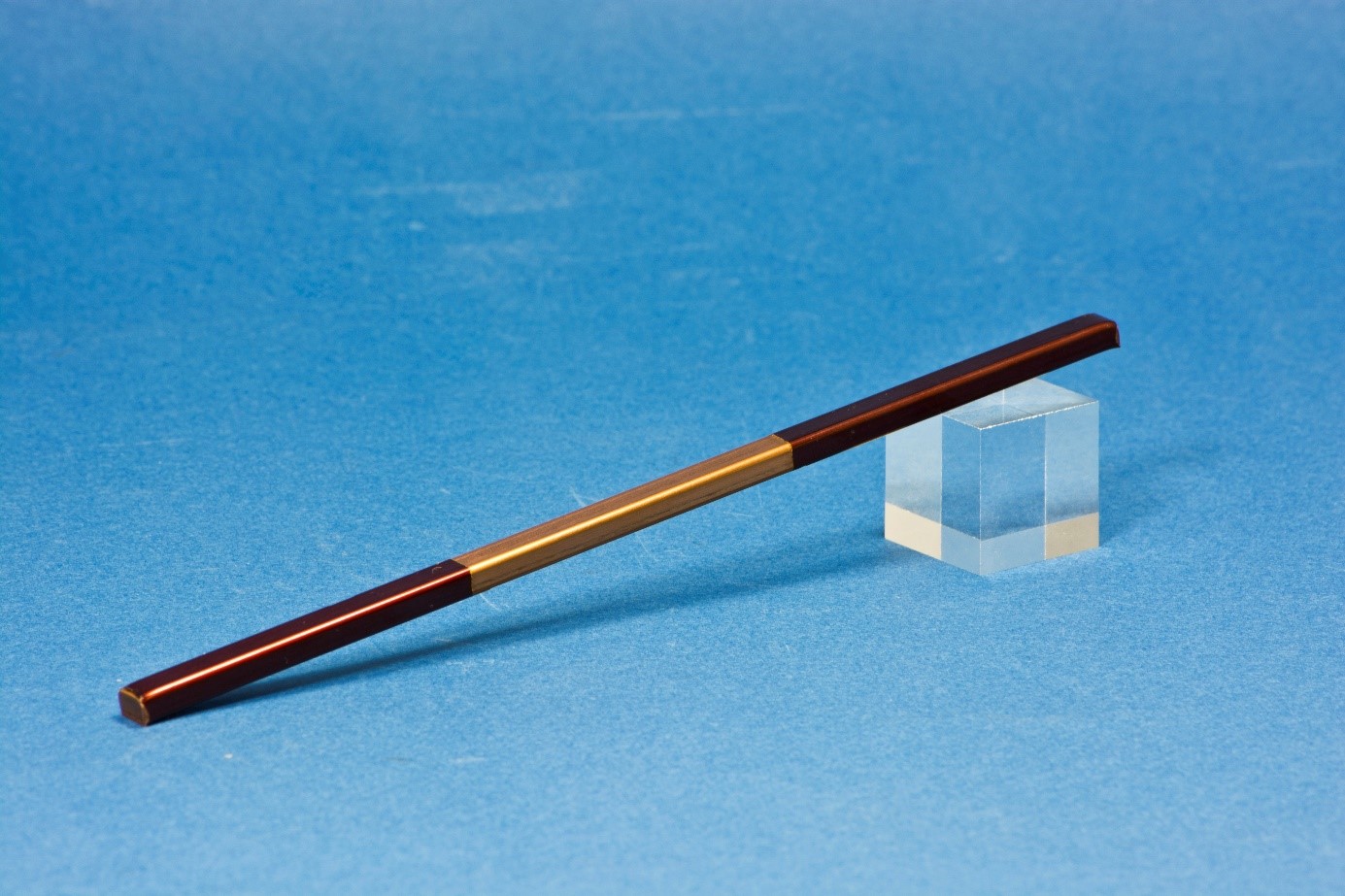
Before large-area coating with e.g. powder coatings, cathodic dip painting or similar, functional areas must be masked or covered in an elaborate manner in order to ensure local clean surfaces for electrical contacting or subsequent joining processes. The reliable control of this procedure and compliance with the quality requirements represent a major challenge.
The demand for locally limited and precise surfaces is predestined for the use of the laser as an ablation tool. In this process, the components are first coated over their entire surface and then the functional areas are exposed. The preparation effort prior to coating is reduced or eliminated and the process becomes more reliable. The coating is then vaporized locally limited to the functional area using the flexible, highly automatable and precise laser tool. The waste products are extracted, filtered and, if necessary, post-treated. Precise control of the laser beam movement and permanent generation of the laser beam ensure consistently high processing quality.
Other possible applications of highly efficient laser beam ablation are the stripping of copper wires for traction motors in the field of e-mobility (Fig. 1) and the local cleaning of joining surfaces before welding or soldering.
In addition to technological investigations to determine the machining parameters for high rate stripping, the Fraunhofer IWS is working on systems engineering solutions for implementation in the manufacturing environment. This includes the selection and qualification of system components as well as the development of control solutions and operating concepts. Based on many years of experience in the field of laser material processing, the Fraunhofer IWS develops customized solutions in the area of high-rate ablation of functional surfaces.